TECHNOLOGIES
PERVAPORATION (PV) & VAPOR PERMEATION (VP)
Pervaporation (PV) and Vapor permeation (VP) are membrane separation techniques which are used to separate or recover components from liquid or vapor mixtures respectively by selective permeation.
Some of the industrial separation problems that can be solved with the use of PV and/or VP are listed below.
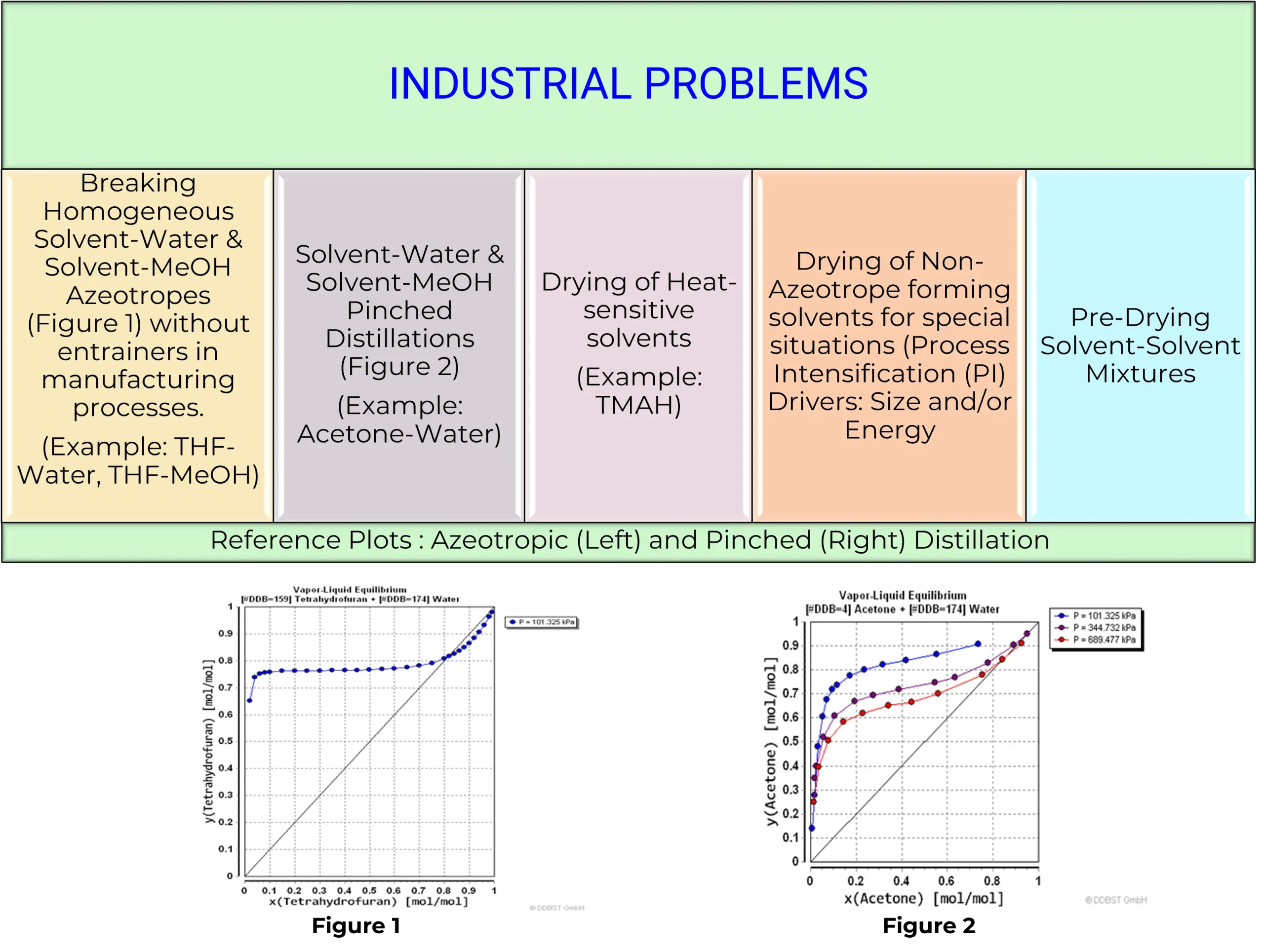
Conventional Technologies & Their Limitations
Simple Distillation:
- Solvent-water mixtures can be easily separated based on relative volatility.
- Simple Batch / Continuous operation can be done.
- Azeotropic mixtures cannot be separated using simple distillation.
Azeotrope / Extractive Distillation:
- Azeotrope or extraction solvent is to be recovered
- GC purity of solvent is reduced
Pressure Swing Distillation:
- Possibility of Solvent Degradation
- VLE Dependent (not multipurpose)
- High Utility consumption
- High Hold-up volume
- Large Footprint
- Long Start-up time
Liquid-Liquid Extraction (LLE):
- Extraction Solvent has to be recovered
- GC purity of solvent is reduced
- Limited applicability
Adsorption / PSA / TSA:
- Media has to be regenerated
- Purge /drain steam is to be treated
- Not suitable for feed with water content more than 1% (for TSA) and more than 5% (for PSA).
- Remains of unidentified trace impurities or trace impurities due to molecular dehydration
- Fine particles due to attrition
Crystallization :
- Depends on the Solid-Liquid Equilibrium.
- Problems with slurries and crystals.
- Limited applicability
Salting Out :
- SLLE based separations
- Salt has to be recovered or high TDS, high COD effluent is to be treated
- Solvent has to be recovered from salt phase
- Possibility of Side Reactions
- Not suitable for drying to less than 1-2% water
- Messy and corrosive effluent to be handled

ZeoSep® Technology
ZeoSep® SolvDry Membrane and Module
• Zeolite Membrane Film hydrothermally grown on Microporous Ceramic Support
• Hydrophilic Membrane with Pore size ~ 0.4 nm
• Adsorption – Diffusion separation mechanism
Key Features: -
High Flux & Super High Selectivity for Water Permeation
High Chemical, Mechanical and Thermal Stability
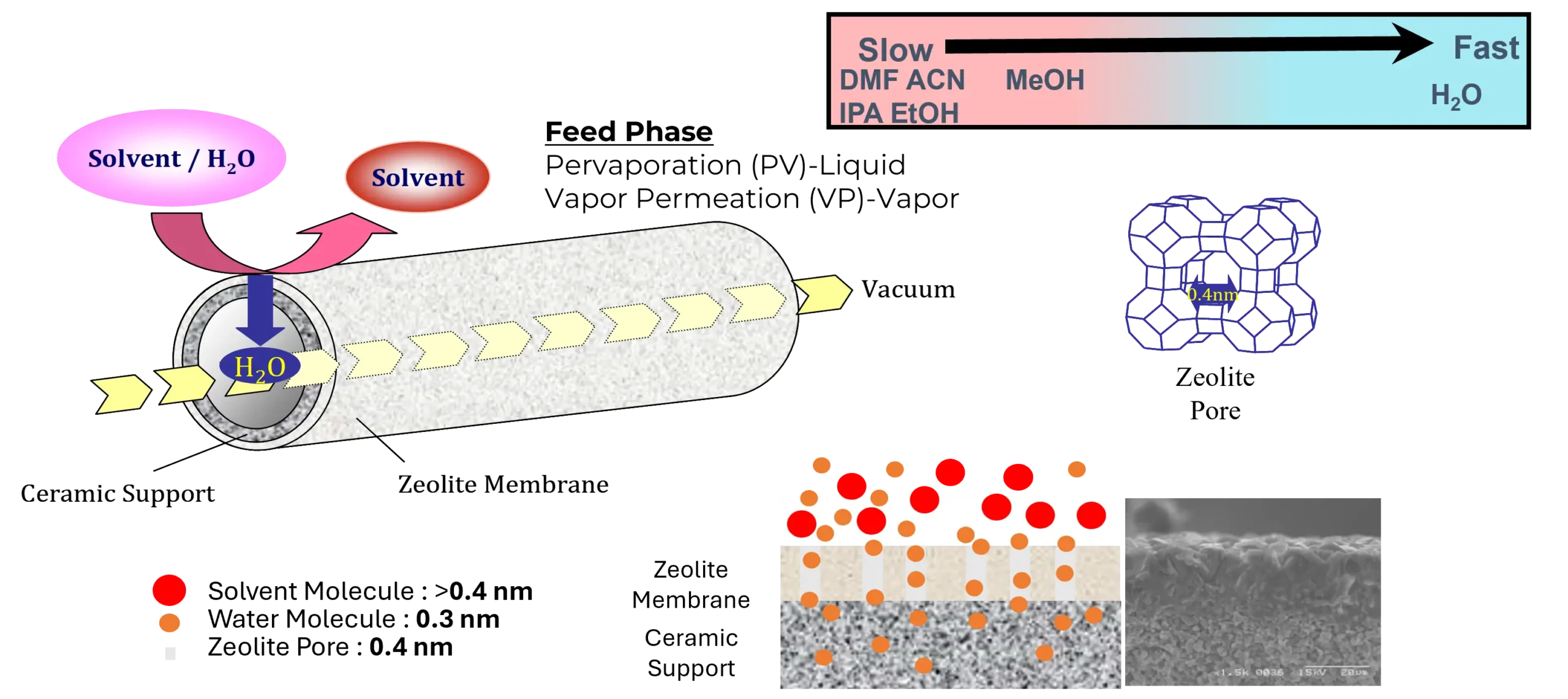
A Multi-pass ZeoSep® SolvDry Tubular Membrane Module is shown below. This module has Efficient Mass transfer and Easy Maintenance.
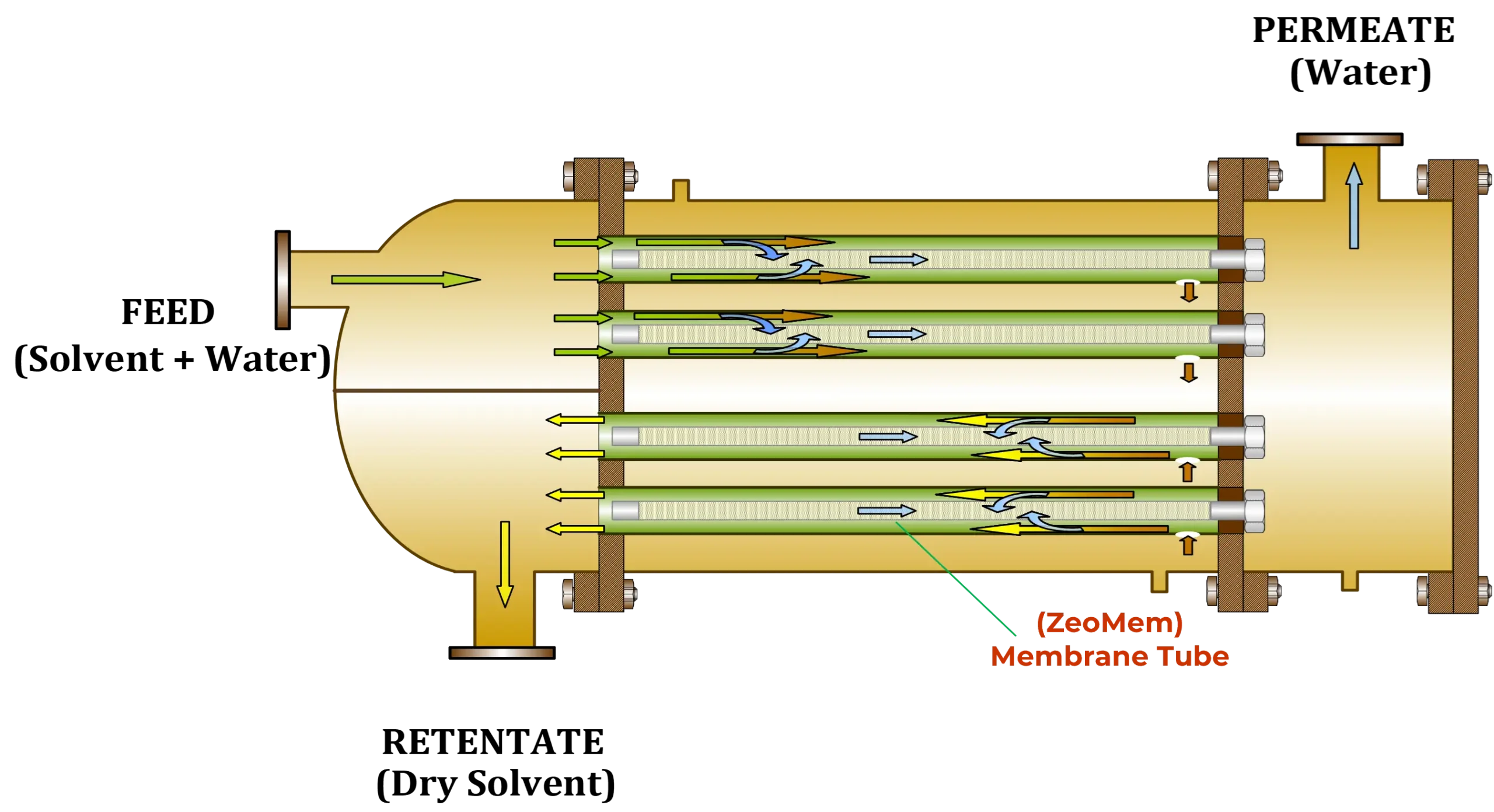
ZeoSep® Pervaporation (PV)
The schematic process flow diagram has been shown for ZeoSep® SolvDry Pervaporation (PV) Membrane System. The Solvent-Water liquid Feed mixture is sent to the PV Membrane Module to separate out water as the Permeate and Dry Solvent as the Retentate.
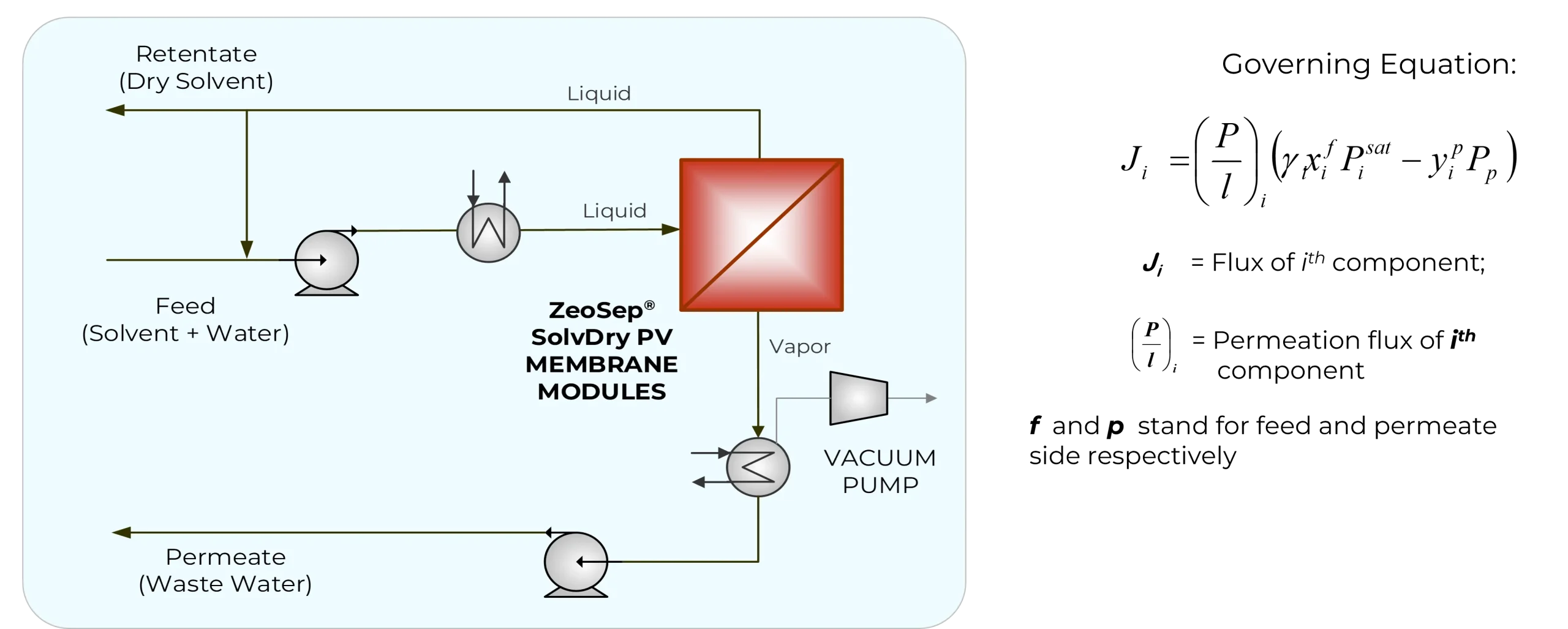
ZeoSep® Vapor Permeation (VP)
The schematic process flow diagram has been shown for ZeoSep® SolvDry Vapor Permeation (VP) Membrane System. The Solvent-Water mixture Feed is vaporized and sent to the Membrane Module to separate out water as the Permeate and Dry Solvent as the Retentate.
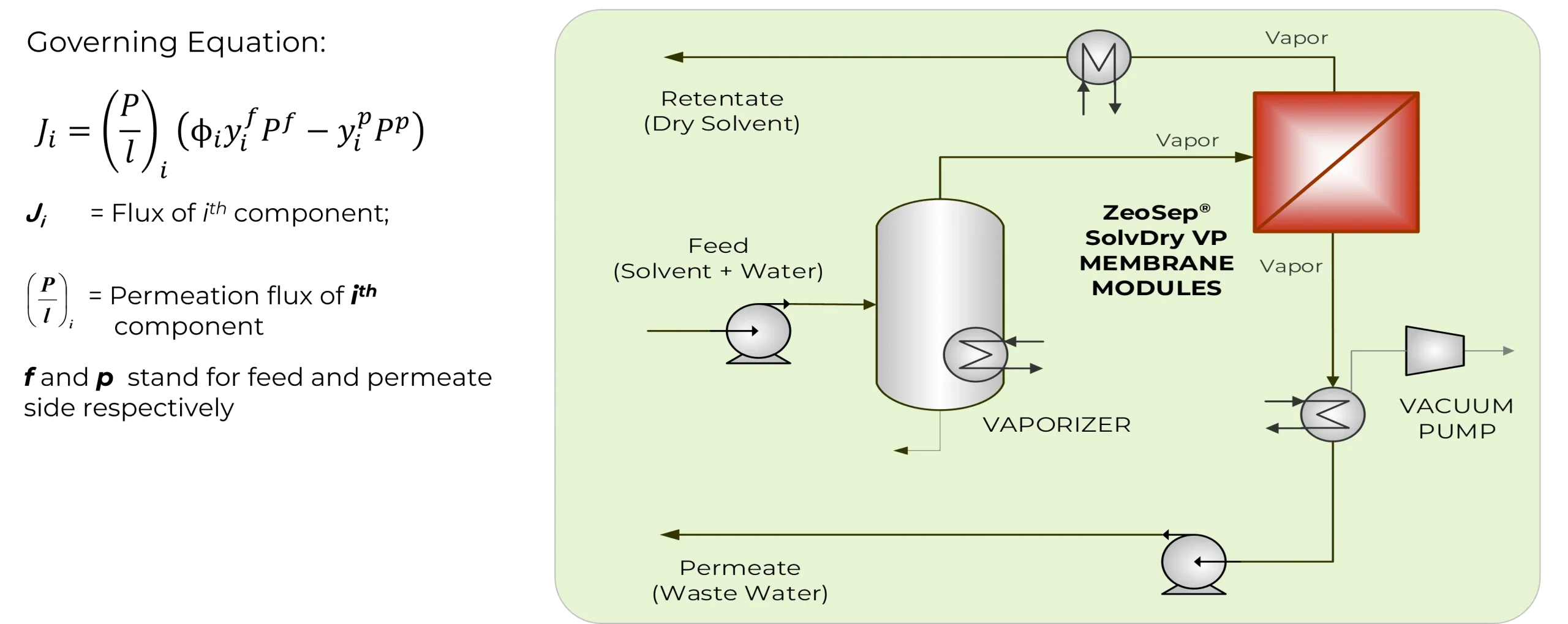
MAREX (MEMBRANE ASSISTED REACTIONS)
MAREX™ for Driving Equilibrium Condensation Reactions to Completion
Our MAREX™ Systems are available in four different modes – wherein they are directly or indirectly integrated with reactions using pervaporation or vapor permeation membranes. As water is continuously removed, reaction speeds up and goes to near completion. Therefore, need for downstream separations and purification of products is drastically reduced or sometimes eliminated.
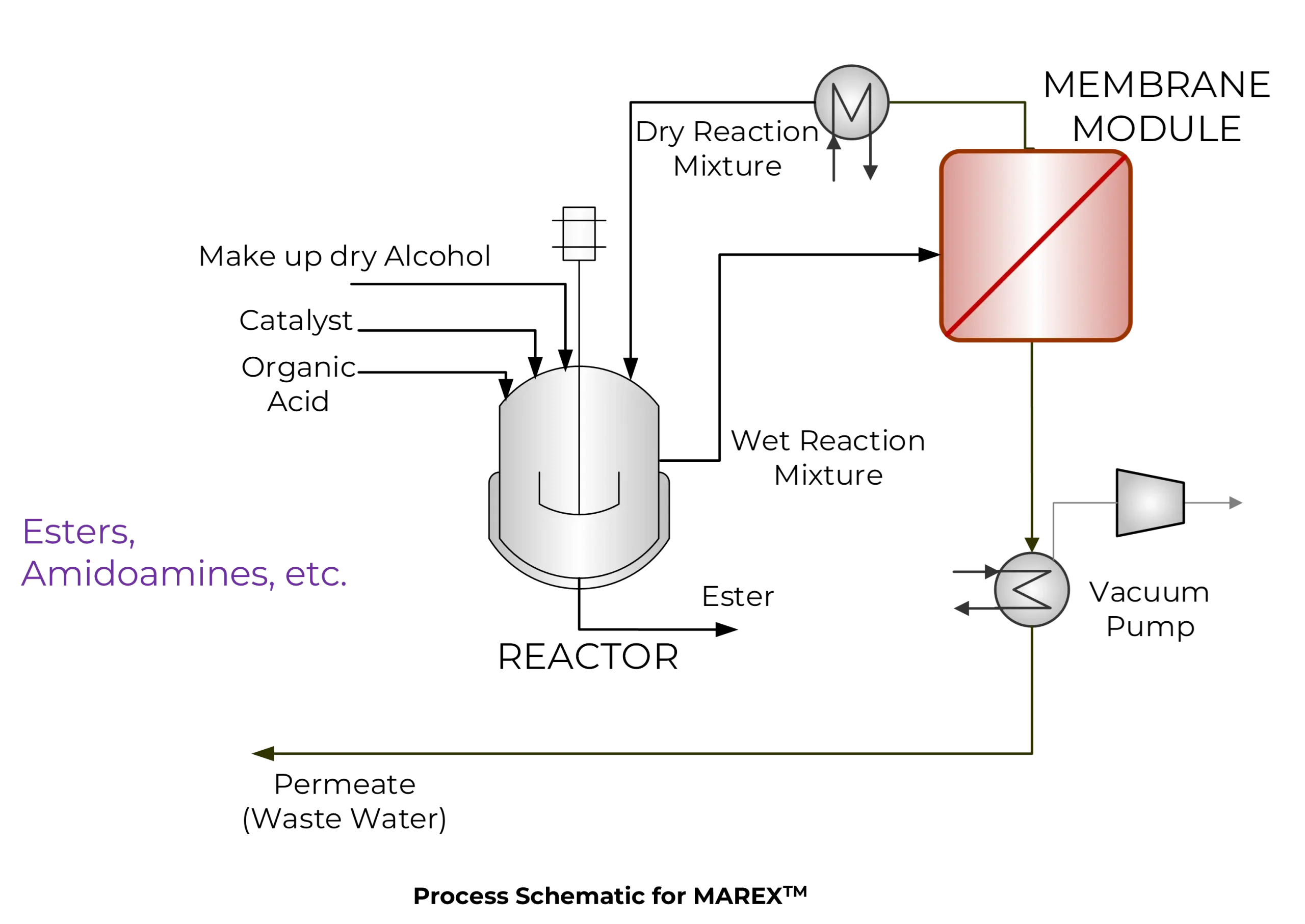
PolyGSep Technology
Solution – Diffusion Mechanism based Polymeric
These membranes are available as : –
Membrane Hollow Fiber
High Flux & High Selectivity
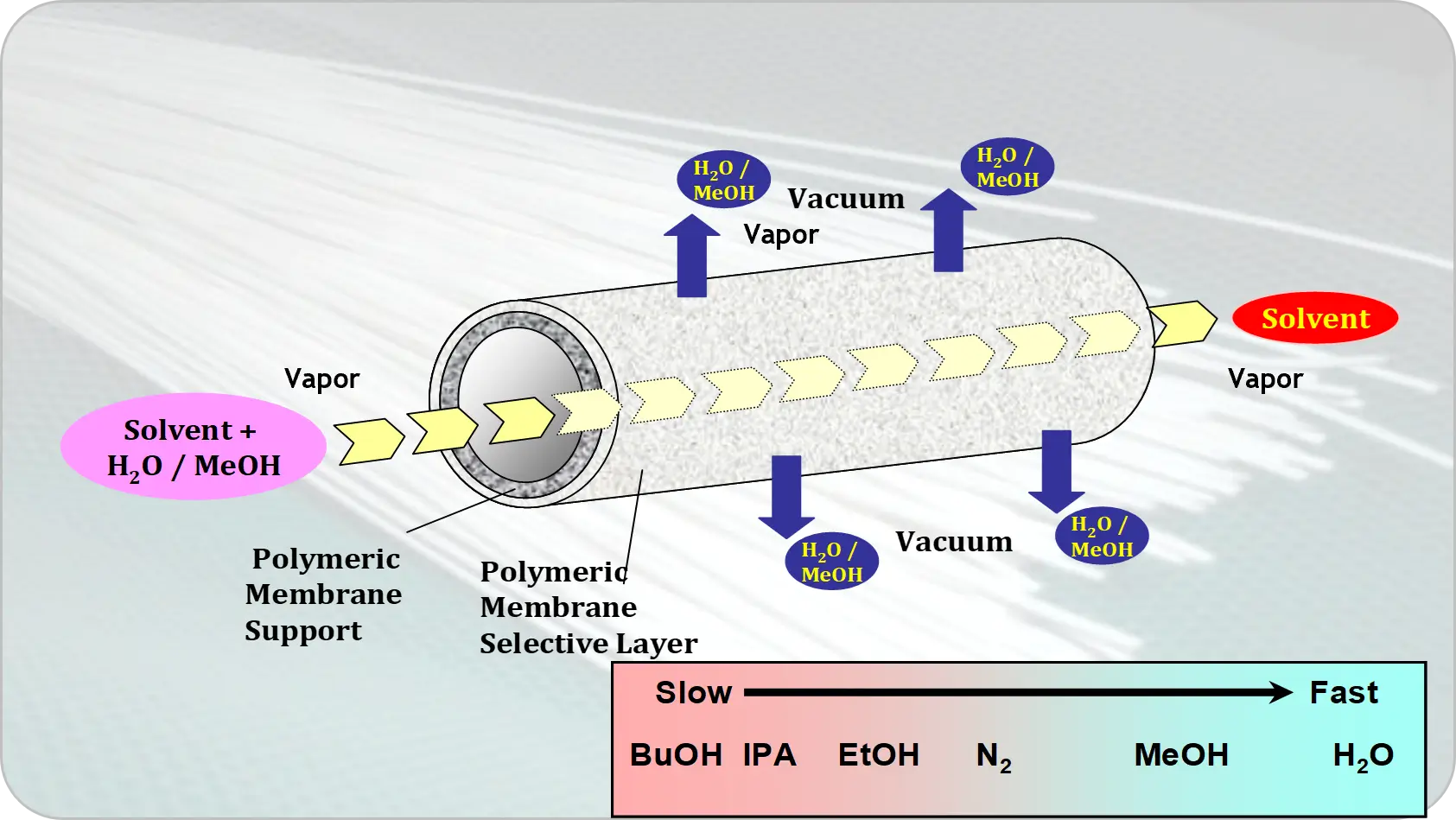
PolyGSep SolvDry Hollow Fiber Membrane Module
Key Features: –
- Compact
- Efficient Mass transfer
- Condensable & Non-Condensable Sweeps to improve the Mass Transfer
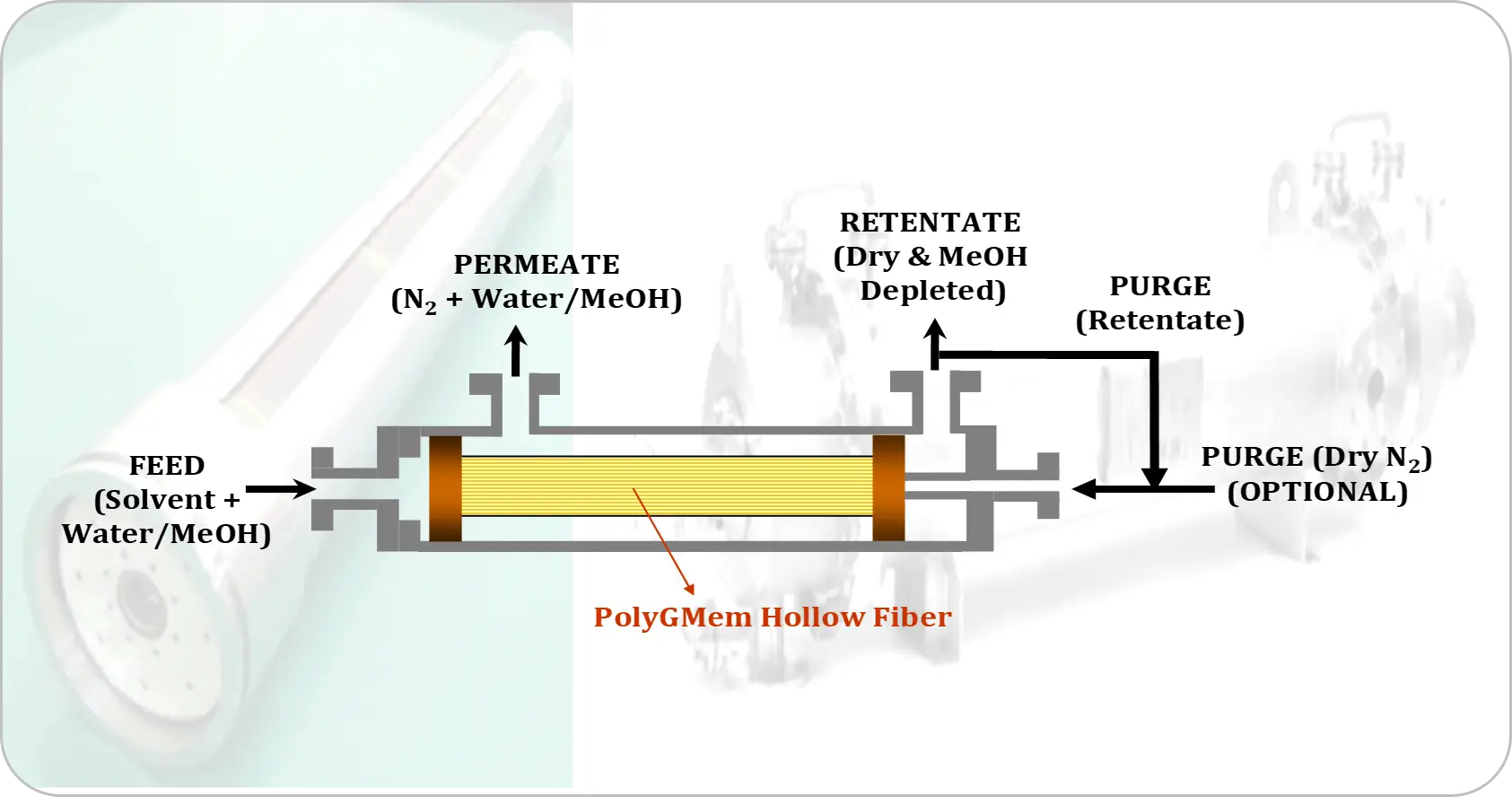
PolyGSep Vapor Permeation (VP)
The schematic process flow diagram has been shown for PolyGSep SolvDry Vapor Permeation (VP) Membrane System. The Solvent-Water mixture Feed is vaporized and sent to the Membrane Module to separate out water as the Permeate and Dry Solvent as the Retentate. In case Methanol is present in the mixture which has to be separated, it can be done using PolyGSep membranes to permeate Methanol out along with water.
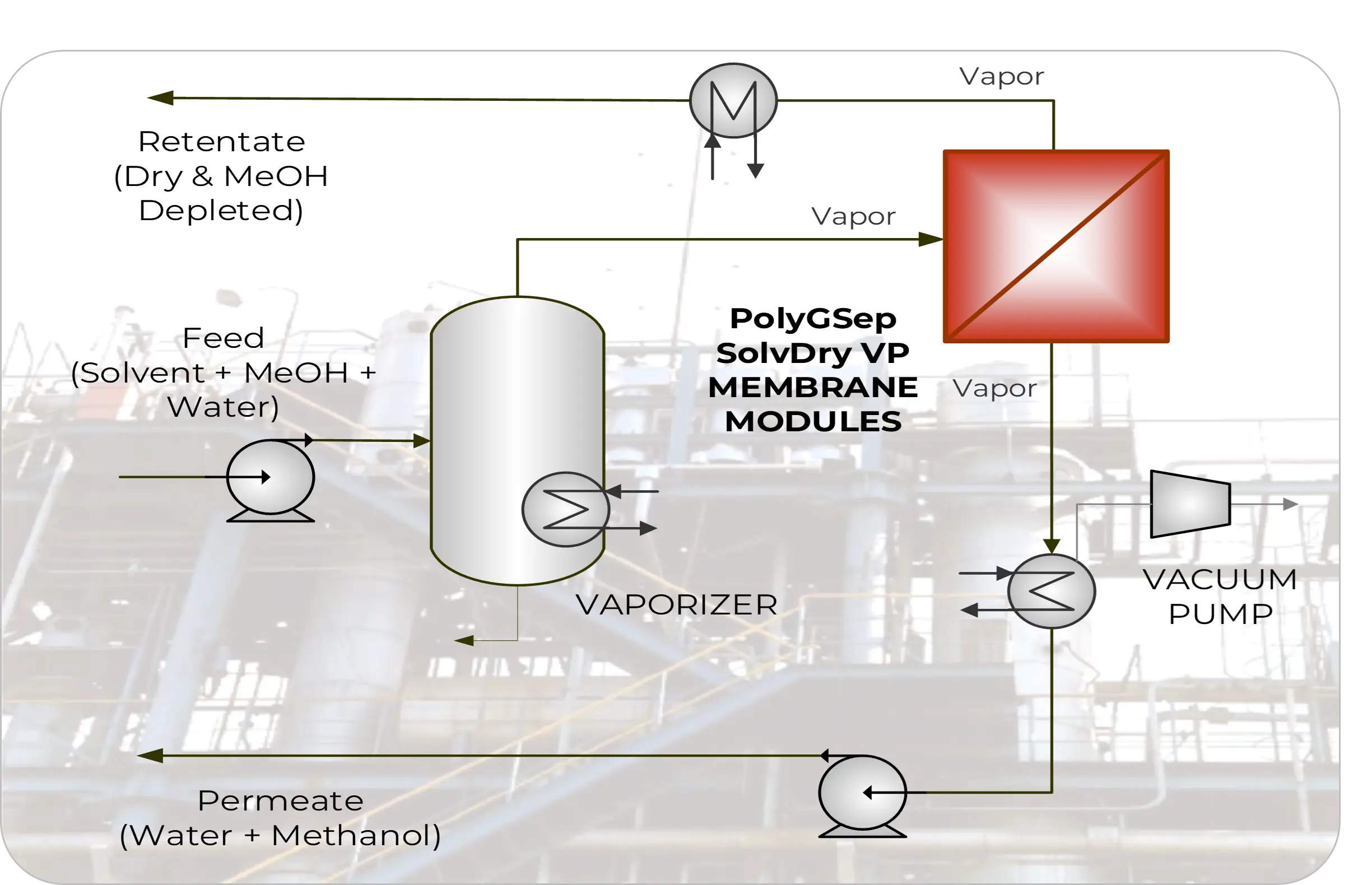
Vapor Permeation (VP) vs Pervaporation (PV)
The fitment of the mode of operation is checked on case-by-case basis. The high-level comparison (for high feed water content) is given in table below:
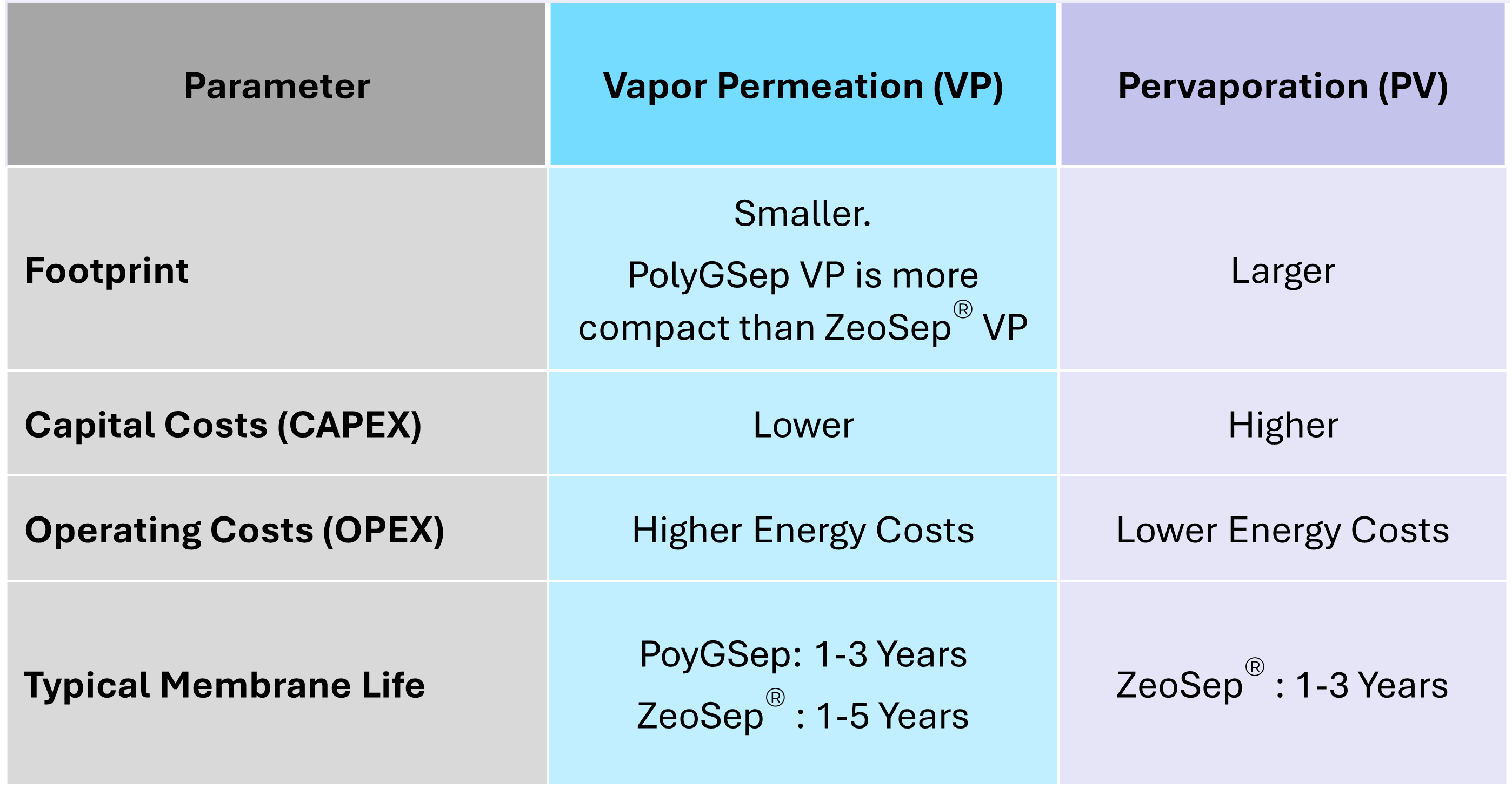
ZeoSep® / PolyGSep Applications
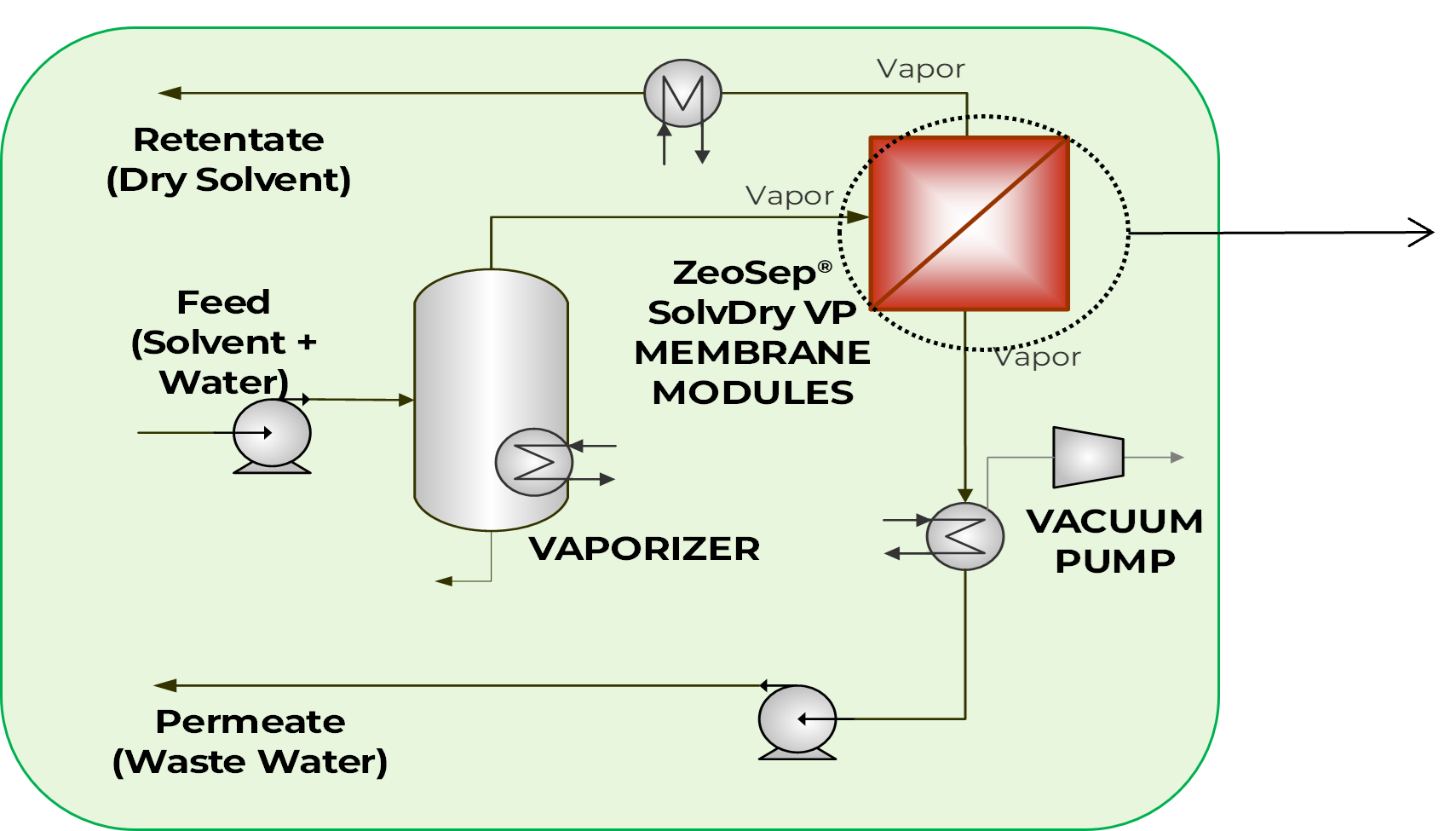
Debottlenecking of distillation columns & adsorption systems
Example- Second distillation column replaced by membrane module to increase system capacity with existing hardware.
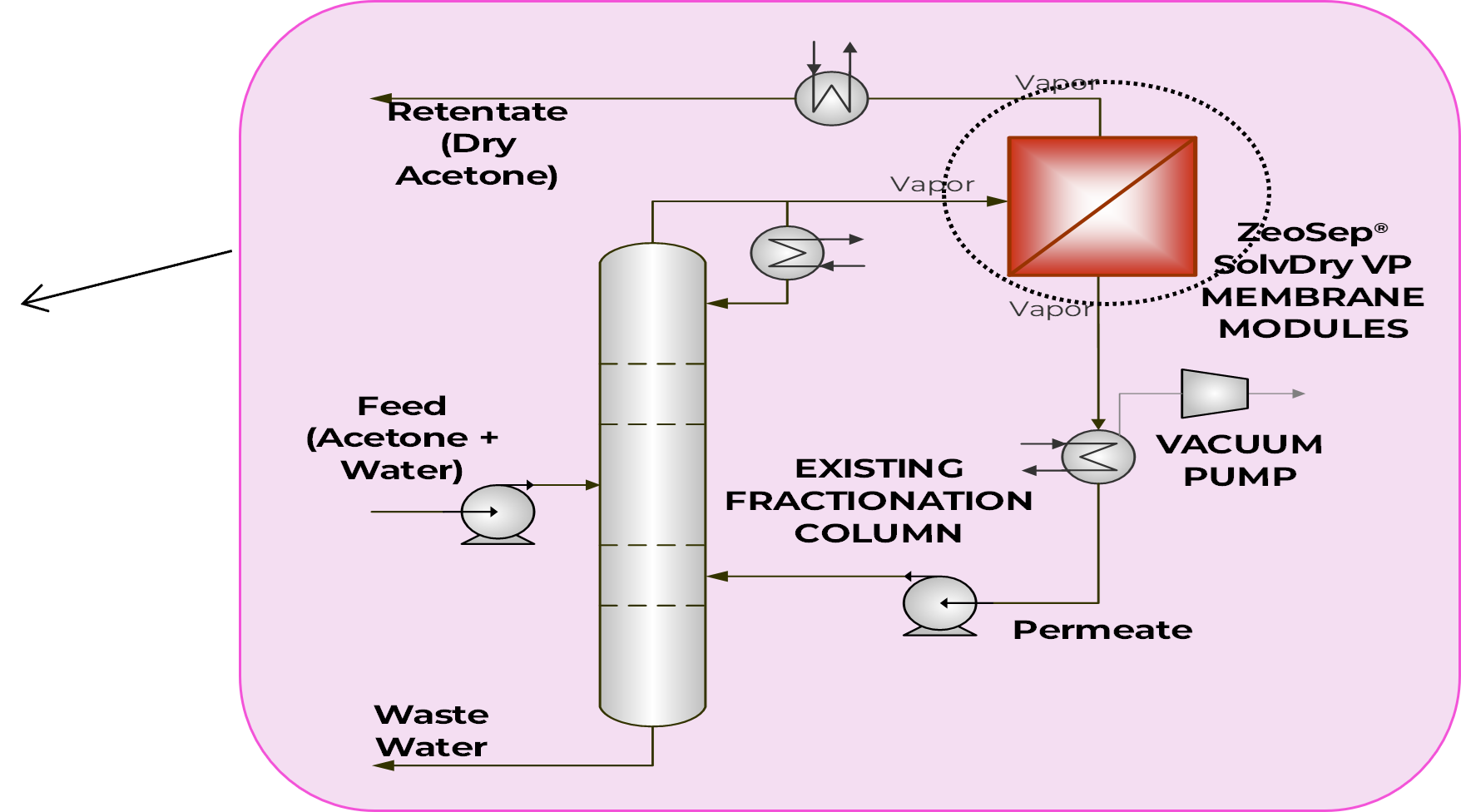
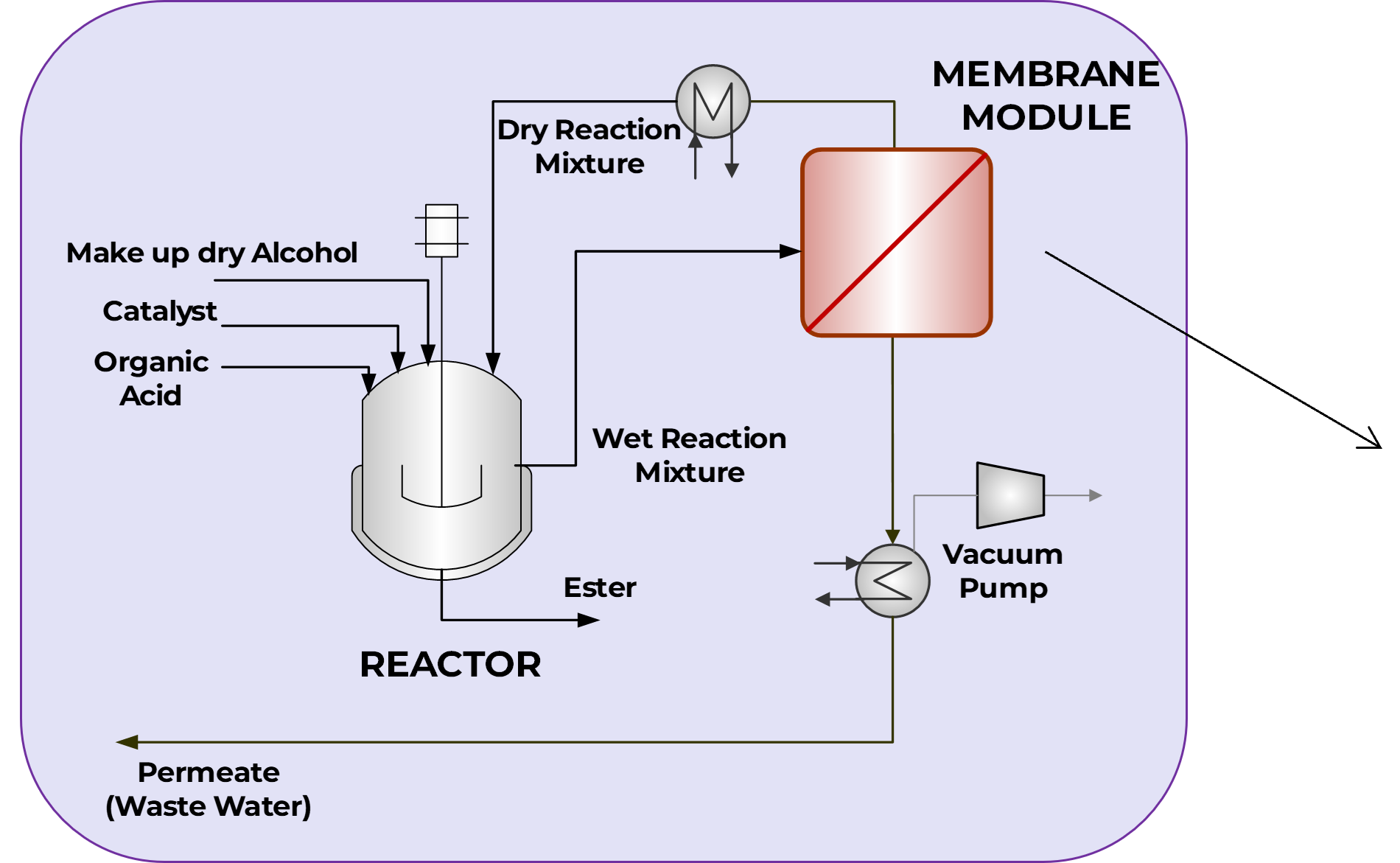
Membrane reactors for in-situ removal of water/methanol in condensation reactions
Example- A Membrane reactor system to enhance condensation reactions.
PolyGSep vs ZeoSep®
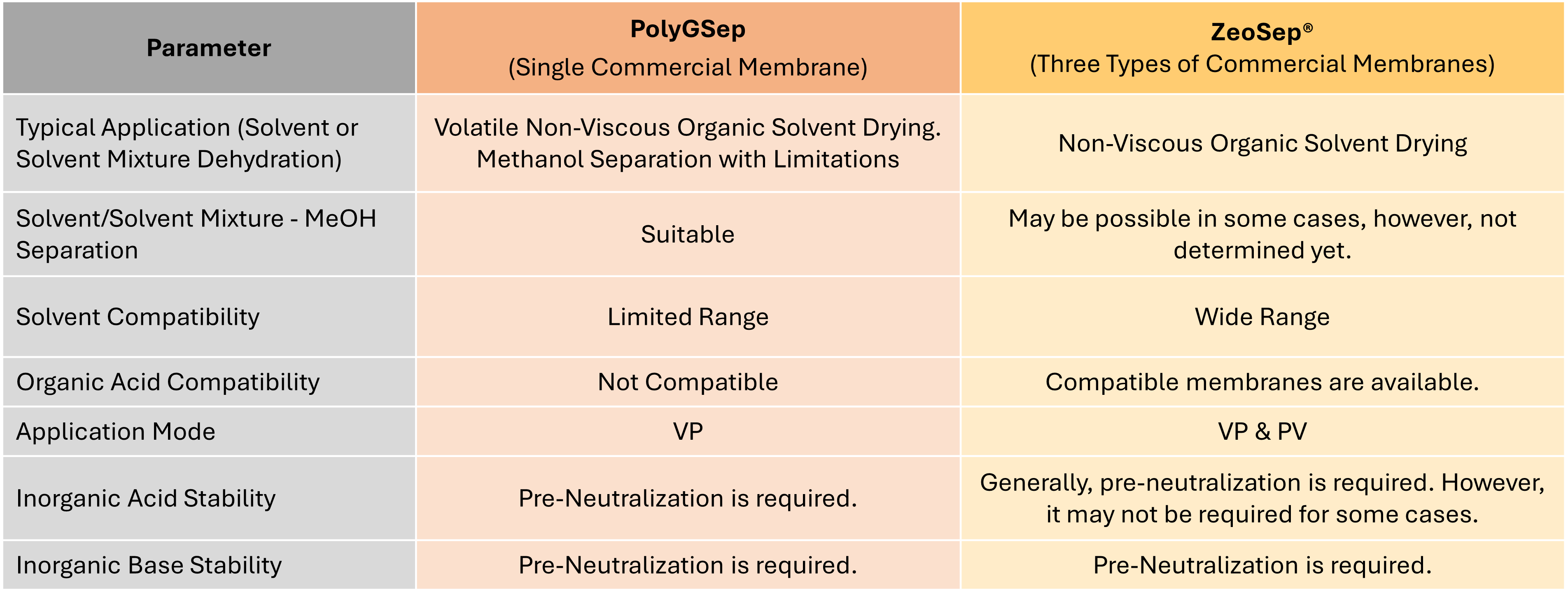
Additional Points:
- Suspended solids and Dissolved solids cannot be fed directly to the membrane. They may be processed in VP system and collected as non-volatile purge, subject to limitations. Else, they need to be removed.
- Water Tolerance is High which can further be improved by integrated distillation operation.
- Solvent Recovery is generally high but need to be judged on case basis. Moreover, recovery can be improved in distillation hybrid systems.
Solvent Compatibility For Drying Of Organic Solvents
Both PolyGSep & ZeoSep®

Alcohols
- Ethanol
- n-Propanol
- Isopropanol
- tert-Butanol
- sec-Butanol
- Allyl Alcohol

Ketones
- Acetone
- Methyl Ethyl Ketone (MEK)

Ethers
- MTBE
- Tetrahydrofuran (THF)
- Diisopropyl Ether (DIPE)
- 1,4-Dioxane-

Esters
- Methyl Acetate
- Ethyl Acetate
- N-Propyl Acetate
- Iso Propyl Acetate
ZeoSep® Only (Not Possible in PolyGSep)

Carboxylic Acids
- Formic Acid
- Acetic Acid

Nitriles
- Acetonitrile
- Propionitrile
- Acrylonitrile

Amines
- Tri Ethyl Amine
- Pyridine

Chloro alkanes
Dichloromethane

Aldehydes
- Propanal
- Butanal

Sulfoxides
- Dimethyl sulfoxide

Amides
- Dimethyl formamide
- Dimethyl acetamide
Alcohols
- Methanol

Pyrrolidones
- N-Methyl-2-Pyrrolidone
Notes:
1. Solvents mentioned above are mere examples within different functional groups. There are many other solvents that can be processed. For any other solvents please contact us.
2. Multicomponent mixture of above solvents can also be processed, as applicable.
CONVENTIONAL & HYBRID TECHNOLOGIES OFFERED
Conventional
Equilibrium Base
- Distillation (Vacuum, Atmospheric, Super-Atmospheric)-Simple, Pressure Swing, Extractive
- Liquid – Liquid Extraction
- Solution Crystallization
- Stripping
- Absorption (Scrubbing)
Adsorption & Ion Exchange Based
- Temperature Swing Adsorption (TSA) [Regenerative and Non-regenerative]
- Ion-exchange
Hybrid
Membrane Based Hybrid Processes
- Membrane – Distillation Hybrids
- Membrane-Adsorbent Hybrids
- Other Hybrids
KEY PROCESS FEATURES
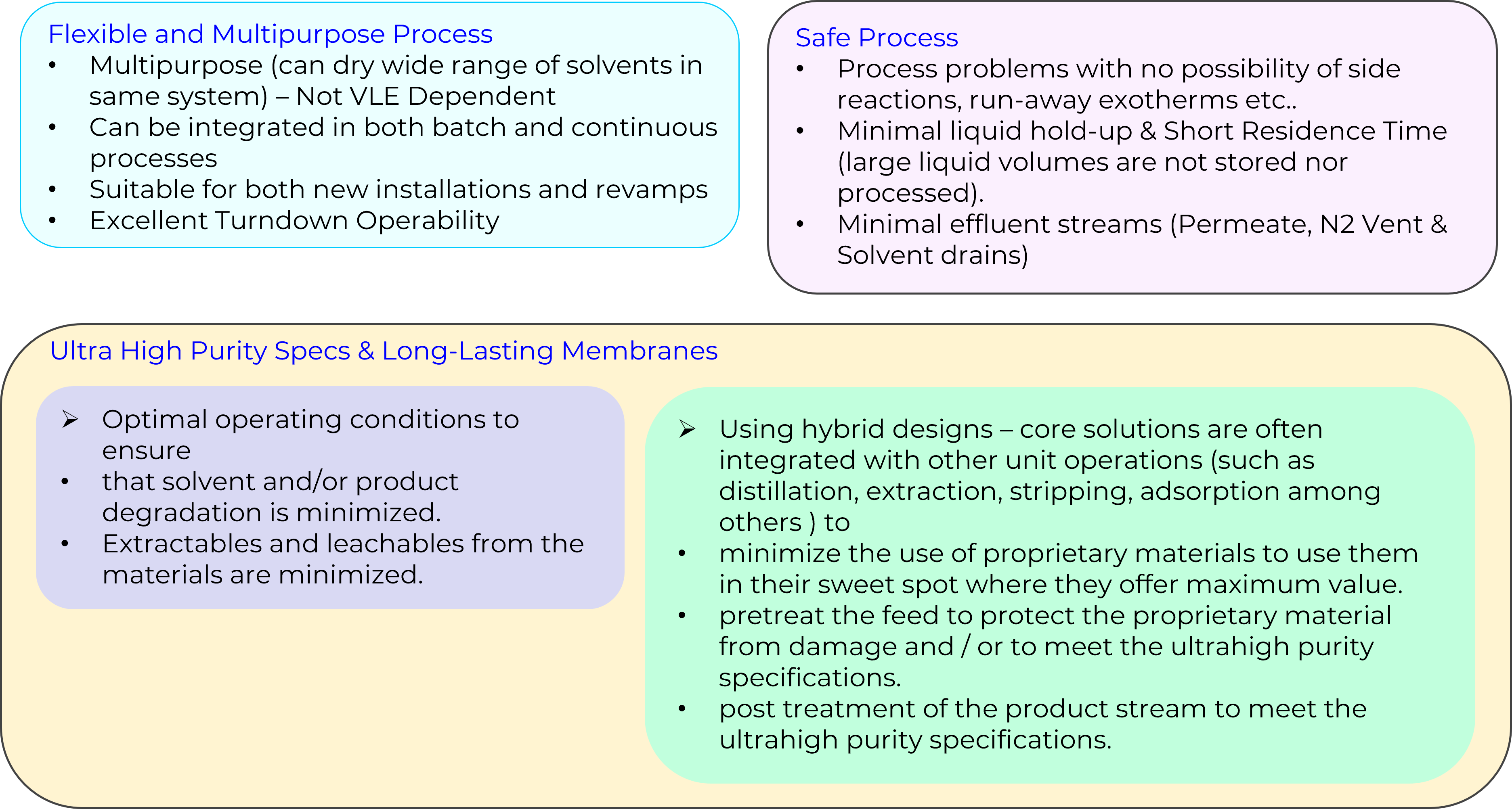
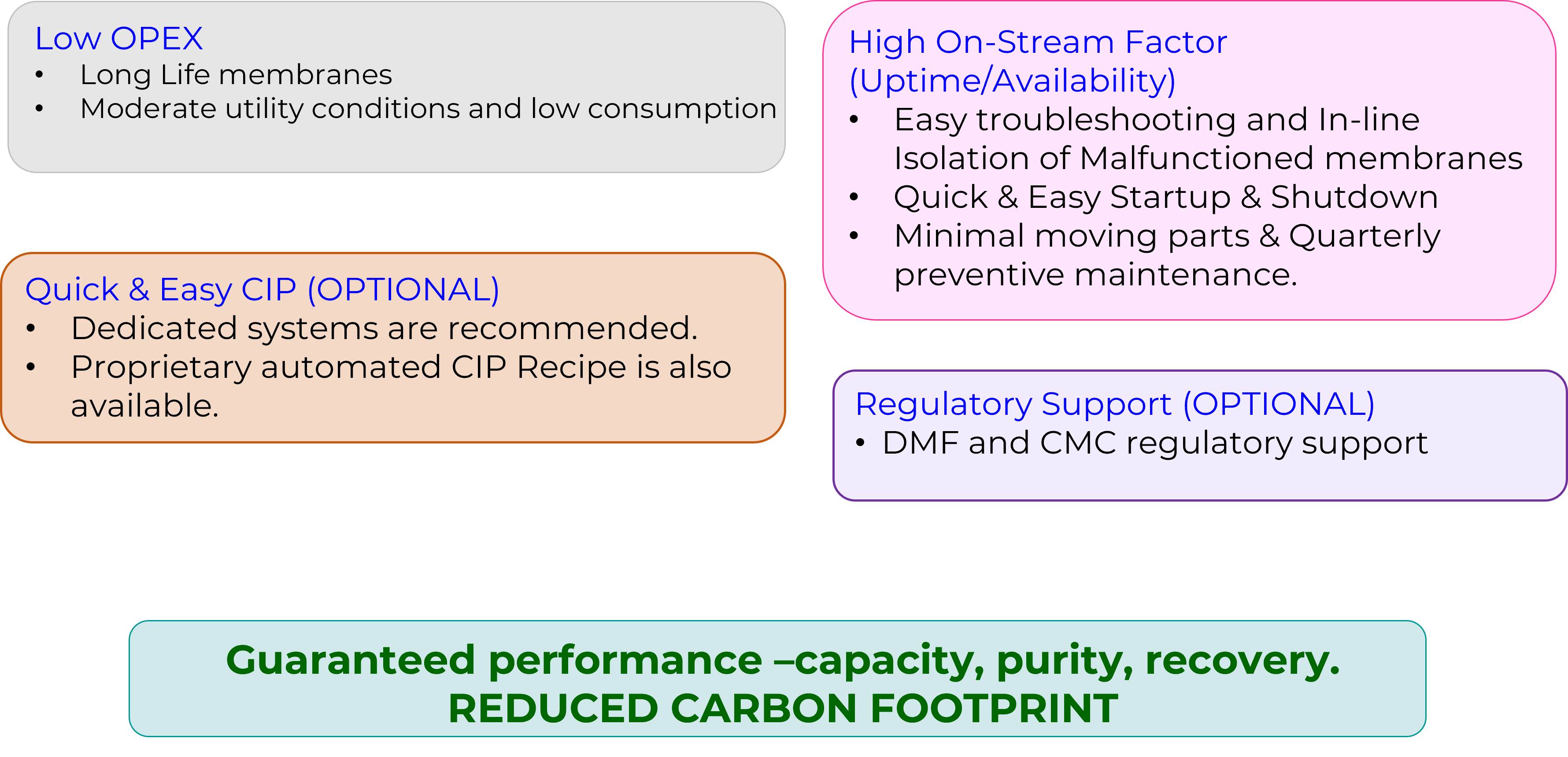
OTHER MEMBRANE SEPARATION PROCESS MODES
We also use following membrane processes whenever there is a compelling case for applying them. Except Gas Permeation, membranes used for these processes are third party membranes. However, process development, design and execution is done in-house.
